The textile industry has a storied history, evolving from traditional hand-weaving methods to highly mechanized production processes. Conventional weaving involved the use of shuttle looms, where a bobbin of yarn was passed back and forth through shed openings. While effective, this method had limitations, including significant material waste and energy consumption.
Enter shuttleless looms: a revolutionary advancement that changed the landscape of textile manufacturing. These modern machines eliminate the need for shuttles altogether, offering greater efficiency and reduced waste. Among the innovations born out of shuttleless loom technology is shuttleless tape — a product designed to optimize textile production further while enhancing sustainability efforts.
Understanding Shuttleless Tape
So, what exactly is shuttleless tape? In essence, it refers to the narrow woven fabrics produced using shuttleless loom technology. Unlike traditional shuttle looms, which require a bulky shuttle to weave, shuttleless looms utilize small, lightweight mechanisms to carry the weft thread across the warp threads. This approach minimizes friction and wear on the materials, leading to fewer breakages and higher quality final products.
The main difference between shuttleless and traditional weaving technologies lies in their operational dynamics. Traditional looms are characterized by frequent stops due to shuttle changes, which results in substantial downtime and inefficiency. Conversely, shuttleless looms operate continuously, significantly boosting productivity and making them ideal for high-speed, large-scale textile production.
Efficiency and Waste Reduction
Sustainability is often synonymous with reducing waste, and shuttleless tape excels in this domain. By design, shuttleless looms cut down on raw material wastage. The precise nature of shuttleless technology means less excess material is needed around edges and seams, ultimately leading to more efficient fabric utilization.
A comparison reveals notable differences—traditional weaving can produce considerable scrap and leftover material that either goes to waste or requires additional processing to repurpose. In contrast, shuttleless weaving drastically lowers these figures, contributing to a leaner, greener operation.
Energy Conservation Benefits
Another critical aspect of sustainable practices revolves around energy usage. Shuttleless tape production shines here as well; shuttleless looms consume less energy than their traditional counterparts. With fewer moving parts and optimized motion paths, these machines reduce overall power requirements during the weaving process.
The environmental dividends are clear: lower energy consumption translates to a smaller carbon footprint for manufacturers. This shift not only aligns with global sustainability goals but also offers tangible cost savings on energy expenses.
Enhancing Material Utilization
Precision is at the heart of shuttleless tape technology. By leveraging advanced control systems, shuttleless looms ensure exact measurements and cuts, minimizing the need for surplus material. This fine-tuned accuracy leads to better material management and reduced dependence on additional raw resources.
Durability and Quality of Shuttleless Tapes
One might ask whether efficiency compromises the quality of the end product. Thankfully, the opposite is true for shuttleless tapes. Fabrics woven using this technique exhibit increased strength and longevity compared to those made with traditional looms. Enhanced durability means these fabrics withstand wear and tear better, resulting in longer-lasting products that reduce the frequency of replacement and associated waste.
Case Studies and Real-World Applications
Numerous companies have successfully implemented shuttleless tape technology, reaping measurable benefits. For instance, renowned brands utilizing Chuangqi Textile Technology Co.'s shuttleless tapes have reported significant reductions in waste generation and improvements in energy efficiency. Such case studies provide concrete evidence of the positive impact this innovation has on both economic and environmental fronts.
Future Prospects and Innovations
As technological advancements continue to emerge, the future of shuttleless weaving looks promising. New developments aim to further enhance the efficiency and sustainability of these systems. Potential breakthroughs include intelligent loom designs capable of real-time adjustments and even smarter resource allocation, bolstering the prospects for an even greener textile industry.
Adoption Challenges and Solutions
Despite its merits, widespread adoption of shuttleless tape technology does face challenges. High initial investment costs and resistance to change within established workflows can pose obstacles. However, incentivizing adoption through policy support and providing detailed cost-benefit analyses can help businesses navigate these hurdles.
Economic Benefits for Manufacturers
Manufacturers stand to gain economically by adopting shuttleless tape technology. Reduced waste and lower energy consumption lead to direct cost savings. Moreover, investing in sustainable practices attracts eco-conscious consumers and adheres to regulatory standards, fostering long-term financial advantages.
Consumer Awareness and Demand
Today's consumers are increasingly mindful of sustainability, driving demand for environmentally friendly products. Shuttleless tape meets this demand head-on, delivering high-quality, durable, and sustainable textile solutions that resonate with conscious buyers.
Policy and Industry Standards
Government regulations play a crucial role in promoting sustainable technologies. Policies encouraging the use of shuttleless looms can expedite their adoption. Additionally, adherence to industry standards and certifications related to sustainable textiles helps firms distinguish themselves in the marketplace.
Call to Action for Stakeholders
The push towards a more sustainable textile industry is a collective effort. We call upon manufacturers to embrace shuttleless tape technology and demonstrate a commitment to environmental stewardship. Collaboration among industry players will amplify the impact, paving the way for an era of more responsible and sustainable textile production.
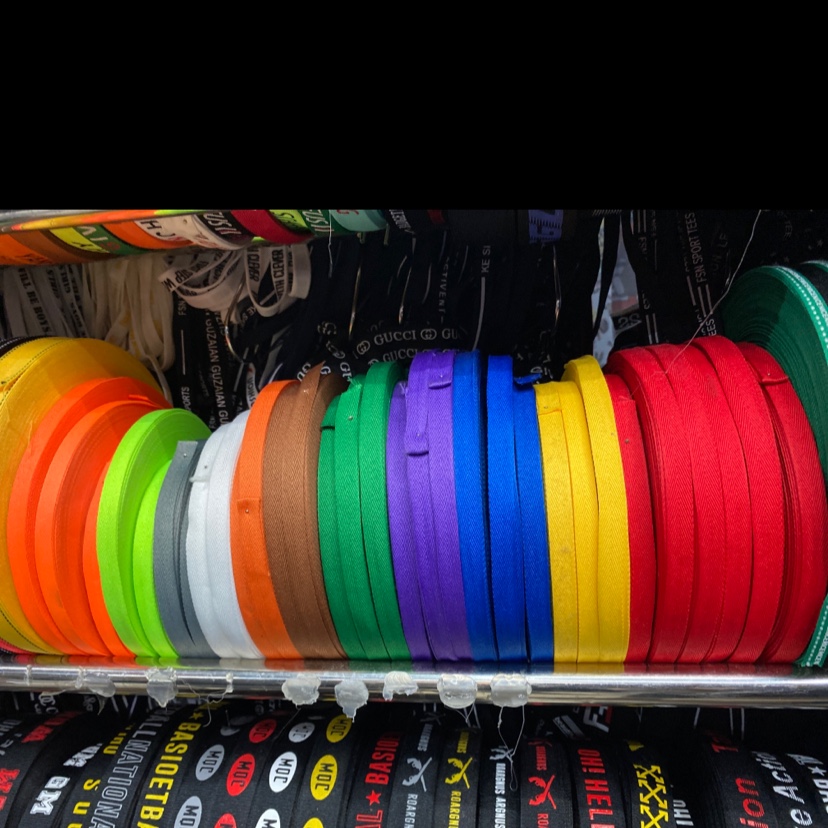